We offer two die-casting service options-die-casting and casting-each option will provide its own advantages according to your project needs. If there are more parts, affordable parts prices are important, and rapid production throughout the product life cycle is essential, then our on-demand manufacturing option will be the ideal choice.
Make molds on demand
Mold price | Higher than prototyping tools |
---|---|
Partial price | Below prototyping tools |
Cavity | Single cavity and multiple cavity |
Guaranteed mold life | unlimited |
Mold storage | Idle for three years |
Quality document | Including molding process development report and basic inspection report; enhanced inspection report can be provided upon request |
Additional functions |
|
Why use on-demand manufacturing tools?
Greenbat Technology's on-demand manufacturing service can help you simplify your supply chain, so that you can get quality parts easier and faster. We use industry best practices such as scientific molding to speed up the manufacturing cycle to shorten your time to market. We meet your inventory needs, there is no minimum order quantity, and provide supply chain flexibility, ranging from bridge tools and just-in-time (JIT) production to production line emergencies.
Run in small batches
- Before mass production, the part design, assembly process and market demand are verified through trial run.
- Inventory overhead is managed through parts production only when demand is determined.
- Used as the main production method for thousands of products sold annually.
Bridge tools
- Implement cost-effective aluminum molds and then commit to using steel molds for capital expenditures.
- Minimize the "waiting cost" of buying steel tools and bring them to the market faster.
Optimize the supply chain
- When repairing large production tools, you can minimize downtime and reduce the risk of out-of-stock.
- Reduce the risk of domestic and global transportation delays by providing reliable suppliers of small quantities of on-demand parts.
- Manage the increase in demand fluctuations without delaying delivery.
reduce manufacturing cost
- Unlock new market opportunities by cost-effectively producing low-volume end-use parts
- Purchase parts on demand without any minimum order quantity (MOQ) requirements
- Reduce inventory costs and storage costs through on-demand procurement.
Data resources

Blog
Magnesium alloy die casting processing manufacturers
Greenbat Technology was established in 2012 and was located in Shenzhen, Guangdong Province. It was a manufacturer specializing in magnesium alloy die-casting.
Read the blog

Blog
Why use magnesium alloy die casting?
When the magnesium alloy material has predictable shrinkage and strong dimensional stability, you can be more certain of the consistency between parts during the entire long-term production process.
Read Blog

Blog
Advantages of die-cast magnesium alloy life
One of the many advantages of die casting is the service life of its magnesium alloy. These commonly used die-cast magnesium alloys have high strength and long service life.
Read Blog

Blog
Process and technical requirements of die-cast aluminum
Three main technologies for the processing steps of cast aluminum parts In today’s society, many processing industries are using the latest processing technology
Read the blog
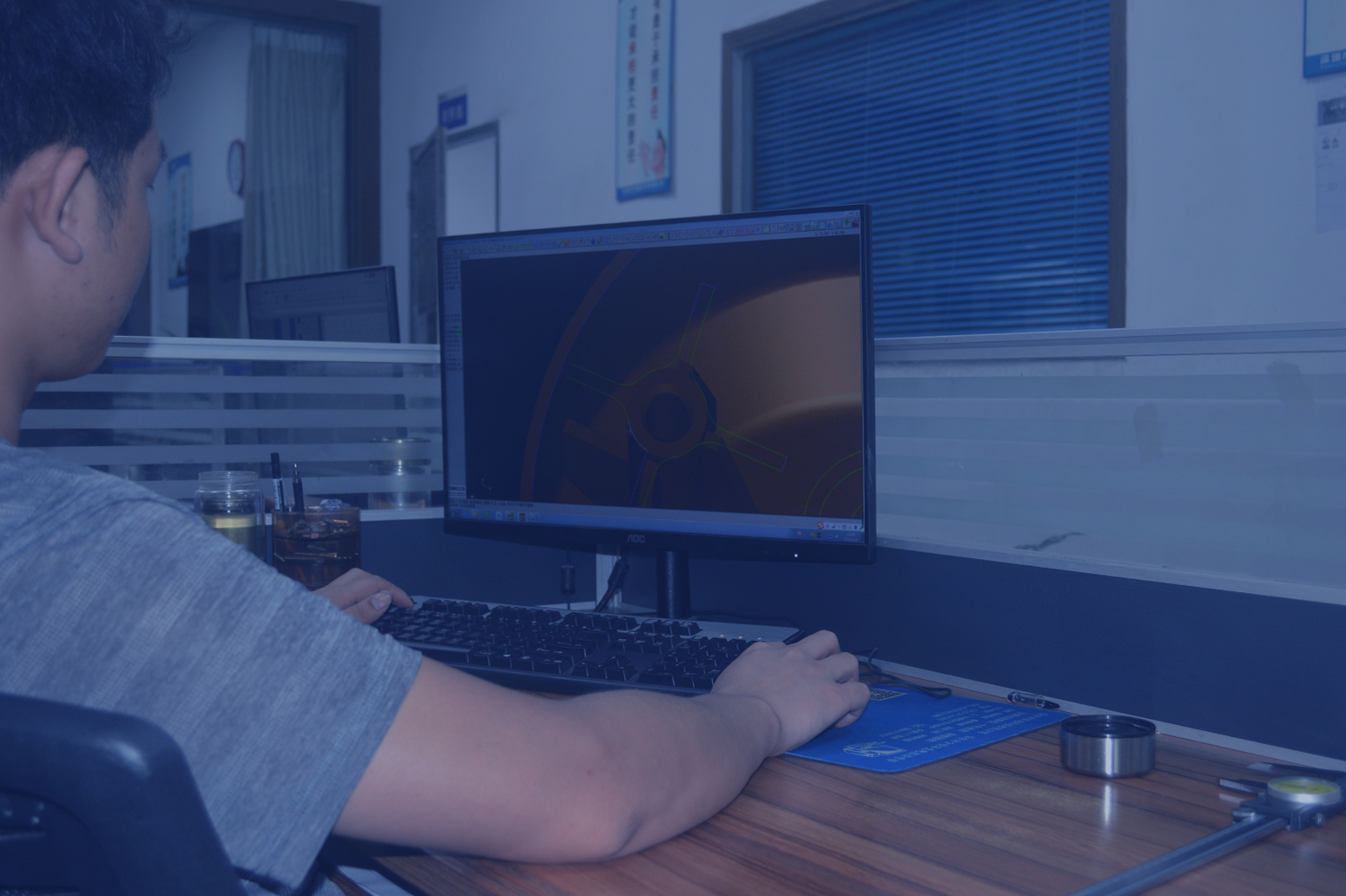